Electric car controllers are used to control the start, operation, moving forward or backward, acceleration/deceleration, stop along with controlling the core controllers of other electronic devices. It acts just like the brain of an electric car and is a critical part of the electric car. Therefore, whether an electric car controller acts normal or not greatly affects the performance and safety of the electric car. As a result, every electric card manufacturer emphasizes on the cooling of electric car controllers.
We adopted water-cooling design for this cooling solution for the electric car controller
The thermal components can be divided into two categories:
There are a frame and a cold plate structure. These two portions will be assembled together at the final stage.
The design allows the back side of the cooling plate to make full contact with the thermal components in order to enhance the heat-transfer efficiency of the cooling area.
Power and contact area of the power devices:
Device (No.)
|
Contact are (mm²)
|
Power (W)
|
1 Rectifier Module
|
1192.99
|
121
|
2 IGBT Module
|
1192.99
|
316
|
3 Resonance Inductor
|
1299.62
|
18
|
4 Output Inductor
|
3363.57
|
16
|
5 Transformer
|
3363.57
|
70
|
6 PFC Module
|
1192.99
|
50
|
7 PFC Module
|
1192.99
|
50
|
8-11 PFC Choke(Each Group)
|
1002.05/Group
|
24/Group
|
Schematic of the meshes for the water-cooling cold plate and cooling tubes:
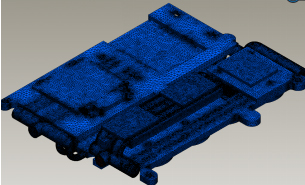
Schematic of the entire electric car controller cold plate:
(Total weight:2.55Kg,Frame:1.7Kg,Cold plate:0.85Kg。)
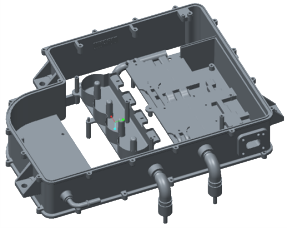
Schematic of the thermal simulation results for the electric car controller:
When the flow rate is:5L/min, Water inlet temperature:25 ⁰C, Water pressure:10485Pa, Highest simulated temperature on the cold plate:46.5 ⁰C。)
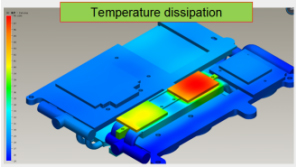
(When the flow rate is:5L/min, Water inlet temperature:65 ⁰C,Water pressure:10500Pa, Highest simulated temperature on the cold plate:86.45 ⁰C。)
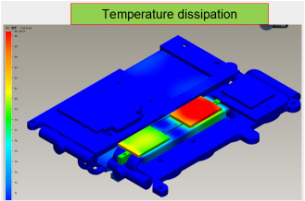